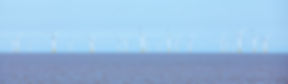
CASE STUDIES
Blackfish Engineering has delivered a wide range of independent and partnership projects, drawing on the experience of our team and the trusted suppliers we work with. We pride ourselves on being small enough to be agile and collaborative, and large enough to deliver projects and solutions of scale.

Mocean
Blackfish have been working with Mocean Energy since 2017, helping them design, fabricate, assemble and commission their Blue X Wave Energy Converter that was installed in Orkney in the summer of 2021. Blackfish were responsible for almost the entire mechanical design and structural assessment.

On Turbine Vessel Charging System
Blackfish had the privilege to work with MJR Power and Automation to develop and test a brand new system to charge electric crew transfer vessels (CTV's, or eCTV's for electrified versions) from offshore wind turbines. This brand new industry will help to reduce one of the largest contributors to carbon emissions associated with offshore wind farm operations, by supporting the electrifying the of the support vessels.

Bombora Wave Power
Blackfish were responsible for the main cell module design in close collaboration with Bombora for their novel mWave device. This work included concept design, attachment mechanism, and auxiliary systems as well as detailed FEA of the structure. Blackfish also completed the development, test rig design and serial manufacture of Bombora's novel air valve system.

Subsea/Offshore Connections
Blackfish have become particularly specialised and experienced in subsea and offshore connections. Specific projects include a yaw clamp for tidal turbines, stab mechanism and foundation electrical connector termination plate (HV, LV and fibre optic wet mate connectors), on turbine electric Crew Transfer Vessel (eCTV) connection system for automated 1000V DC vessel charging (totally hands free) and the novel C-DART connection system.
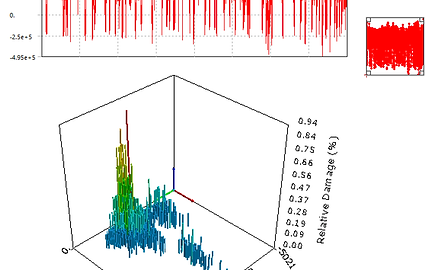
Fatigue assessment of WTG secondary steel-work
Blackfish were brought into a project to assist with a critical fatigue issue on secondary steel-work on a leading wind turbine manufacturer. An expedited solution was a priority for the client, and the team used their skills gained from design and build experience, and worked tirelessly to brainstorm ideas that could develop into workable concepts. Detailed FE fatigue analysis was used to aid with the down-selection process, before presenting the concepts to the client. The success of this work demonstrates how well the Blackfish team can interact directly with both other consultants, clients and stakeholders at all levels.

Finite Element Analysis
Our primary tool for analysing components is Ansys Mechanical. We also have Autodesk’s Nastran software that makes iterations in the design very quick to check before going further. Our team is capable to analyse very complex geometry with multiple connections, joints, welded penetrations.

Southampton Platform and Flow rig
Southampton University now have two test rigs designed and built by Blackfish: a towing tank mooring platform and a pipe flow rig. Blackfish completed the entire concept design, detailed design, structural analysis, and manufacture, as well as transporting it to Southampton to install and commission it ourselves.

Airbus Rig
Blackfish have developed a test rig to allow our client to test hydrogen fuel cells suitability for the aerospace industry. The electrification of aeroplanes is a key target to reduce emissions, particularly damaging at altitude. The test table is able to pitch and roll a 500kg fuel cell to angles up to 50 degrees.